All-In-One Wood Buffing Station Kit for Superior Finishing
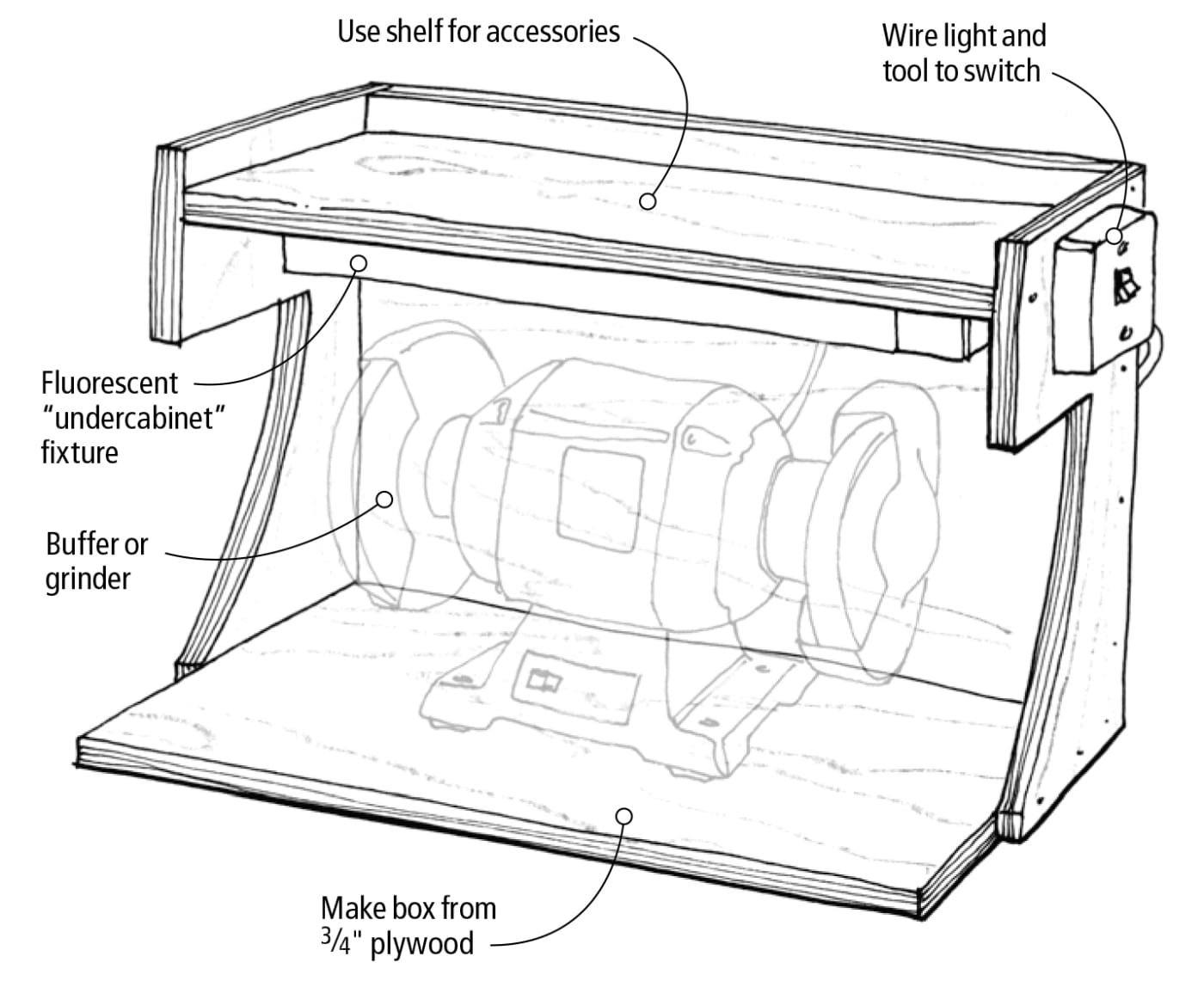
The Ultimate Guide to Tool Sharpening for Woodworking Enthusiasts
We may receive a commission when you use our affiliate links. However, this does not impact our recommendations.
Hey there, fellow woodworking enthusiasts! Whether you’re a seasoned craftsman or a budding DIYer, nothing is more satisfying than working with tools that are as sharp as your ideas. After over 20 years in the woodworking world, I’ve learned that a finely tuned tool isn’t just a luxury – it’s an absolute necessity for precision and safety. Today, I’m excited to share my personal journey with tool sharpening and deliver expert tips and recommendations that will help you elevate your woodworking game. So, let’s dive in!
Why Tool Sharpening Matters in Woodworking
Imagine trying to carve a beautiful curve in a piece of wood with a dull blade. Frustrating, isn’t it? Sharp tools not only make your work easier, they also increase accuracy, reduce accidents, and give a professional finish to your projects. In woodworking, every cut counts, and every tool’s edge tells a story—a story of care, precision, and passion.
The Role of Sharp Tools in Enhancing Your Craft
When your chisels, saws, and planes are razor-sharp, you can enjoy:
- Smooth, clean cuts: Perfect joints and seamless finishes.
- Increased control: Minimum effort with maximum precision.
- Reduced risk of accidents: Less force means safer handling.
- Efficient material usage: Maximizes the potential of every piece of wood.
This isn’t just about aesthetics—it’s about creating a sustainable, repeatable process that makes your workshop a hub of productivity and creativity.
Getting Started: Essential Sharpening Tools and Equipment
Before we get into the nitty-gritty, let’s talk about what you need in your workshop to keep those tools honed to perfection. Over the years, I’ve experimented with various sharpening tools, and here’s a breakdown of the essentials you should consider:
Tool | Use | Pros | Cons |
---|---|---|---|
Whetstones (Oil/Water) | General tool sharpening | Affordable, versatile, precise control | Requires practice; regular maintenance needed |
Diamond Stones | Restoring chipped edges | Quick material removal, durable | Higher upfront cost |
Bench Grinders | Initial shaping | Fast and efficient, great for heavy-duty tasks | Risk of overheating tempered steel |
Honing Guides | Maintaining consistent angles | Ensures precision, ideal for beginners | Limited to specific tools |
Insert image of a well-organized sharpening station here.
My Sharpening Journey: Lessons Learned Along the Way
Every woodworker has that “aha!” moment when they realize the difference a sharply honed tool makes. I remember the first time I decided to invest in a set of high-quality whetstones. My tools went from barely usable to fantastic in just a few sessions. That was the turning point—understanding that regular sharpening wasn’t a chore, but rather an essential part of my craft.
Here are some insights from my journey:
- Take your time with each tool: Rushing the process can lead to uneven edges.
- Invest in quality tools: A good whetstone or honing guide will pay off in the long run.
- Experiment with techniques: Sometimes unconventional methods yield the best results.
- Learn from your mistakes: Every mis-sharpened edge teaches you something new.
Remember, it’s not just about making a tool sharp—it’s about perfecting your technique and understanding the material you work with.
Step-by-Step Guide to Sharpening Your Woodworking Tools
Step 1: Assessing Your Tool’s Condition
Before picking up your sharpening stone, take a moment to inspect your tool. Ask yourself these questions:
- Is the tool’s edge chipped or worn out?
- Does it feel uneven when I run my fingers along the blade?
- What angle was previously used for sharpening, and is it consistent?
This initial assessment helps determine the right approach and abrasives needed for a successful sharpening session.
Step 2: Selecting the Right Sharpening Stone
Choosing the correct stone will depend on the tool and the type of metal you’re working with. For example:
- High Carbon Steel Tools: Often prefer oil stones because they prevent rust.
- Stainless Steel Tools: Water stones work best, offering a sharper finish.
- Dull Edges or Chips: Start with a diamond stone for aggressive material removal, then finish with a whetstone.
As you explore the market, you might notice a variety of options available through affiliate links. Trust me, investing in quality sharpening tools (even if they cost a bit more) will make all the difference in your woodworking projects. Check out some highly rated options below!
Step 3: Sharpening Technique and Angles
One of the trickiest parts of sharpening is maintaining a consistent angle. Here’s how you can do it:
- Use a honing guide: A simple tool that helps you maintain a steady angle, particularly useful for chisels and plane irons.
- Practice with freehand techniques: With experience, many woodworkers prefer the feel of freehand sharpening. It allows for more control when transitioning between different sections of the blade.
- Build muscle memory: Regular practice ensures that maintaining the desired angle becomes second nature.
Insert image of a chisel being sharpened with a honing guide here.
Step 4: The Sharpening Process – A Detailed Walkthrough
Let’s break down the sharpening process into simple, manageable steps:
- Lubricate your stone: Depending on the type of stone, use water or oil. This prevents metal particles from clogging the stone’s surface.
- Establish your angle: Use a honing guide or maintain the angle by careful freehand movement. A commonly recommended angle in woodworking is between 25° and 30°.
- Begin with the coarse side: Start on the aggressive side of the stone to remove any nicks or rough spots.
- Move to the finer grit: Once a substantial portion of the material has been removed, transition to the finer grit for honing the edge.
- Test the sharpness: Use a piece of paper or gently run your thumb (without applying too much pressure) along the edge. A perfectly sharp edge should catch the paper without tearing it.
This systematic approach ensures a balanced, uniform edge that will make your woodworking tasks smoother and more enjoyable.
Common FAQs About Woodworking Tool Sharpening
Q1: How often should I sharpen my woodworking tools?
A: The frequency depends on usage. If you’re using your tools daily, a monthly maintenance schedule might be ideal. For occasional use, inspect the edge regularly and sharpen as needed. The key is consistency—regular inspections prevent minor dullness from becoming a major issue.
Q2: Can I sharpen power tools at home?
A: Most power tools come with replaceable blades or an adjustment system for blade sharpness. However, for tools like table saws, the general advice is to let professionals handle blade sharpening due to the precision required. DIY sharpening can be done, but only if you’re confident in your technique and have the right equipment.
Q3: What’s the best way to store my sharpening stones?
A: Always rinse and dry your stones thoroughly after each use to avoid rust or degradation. Store them in a dry, stable environment and use a protective case or stand to prevent accidental damage.
Q4: Are there alternatives to traditional sharpening methods?
A: Absolutely! Many modern woodworkers explore electric sharpeners and ergonomic grips designed to provide consistent results with less manual labor. However, these tools should complement rather than replace traditional methods, especially when precision is paramount.
Advanced Sharpening Techniques for the Ambitious Woodworker
Once you’ve mastered the basics, it’s time to experiment with more advanced techniques that can further refine your tools:
- Burr Formation Monitoring: Pay close attention to the burr (a small fold of metal created during the sharpening process) as an indicator of edge sharpness. Aim to remove or refine it for an ultra-sharp finish.
- Micro-Beveling: Adding a micro-bevel (a secondary, smaller bevel along the primary edge) can enhance durability and improve cutting performance. This technique requires precision and a steady hand.
- Polishing the Edge: For certain applications, polishing the edge with a leather strop helps achieve a razor-sharp finish. This is particularly useful for fine woodworking or detailed carving projects.
Insert image of a woodworker using a strop for polishing here. These advanced techniques are a testament to how much artistry can be involved in the craft of woodworking, where even the smallest details have a big impact on the final result.
Maintaining Your Entire Workshop: Beyond the Blade
While sharpening your tools is essential, it’s equally important to maintain your overall workspace. A well-organized, properly maintained workshop not only improves efficiency but also enhances the quality of your work.
- Tool Organization: Keep your tools in an easily accessible layout. Consider wall-mounted racks or dedicated cabinets for sharp and delicate equipment.
- Cleanliness: Dust and debris are the enemies of precision. Regularly clean your workbench and workshop floor to avoid any grit that might dull your freshly sharpened tools.
- Proper Lighting: Good lighting can help you see details, ensuring precision during both your sharpening and woodworking tasks.
- Safety Precautions: Always use protective gear such as gloves and safety glasses. Remember, even with sharp tools, safety should be your top priority.
This commitment to workshop maintenance reflects the broader mindset of a dedicated woodworker—always aiming for excellence in every aspect of the craft.
Recommendations and Affiliate Links That I Trust
Now, I’d like to share some of my favorite sharpening tools and accessories that have stood the test of time in my workshop. These items are carefully selected based on performance and reliability. And yes, if you purchase through any of the following affiliate links, I may receive a small commission. Rest assured, these recommendations are unbiased and based solely on my experience.
- Quality Whetstone Set: Ideal for all-purpose sharpening. Look for a set that includes coarse, medium, and fine grits.
- Diamond Sharpening Stone: Perfect for restoring chipped or heavily dulled edges.
- Honing Guide: Essential for maintaining consistent sharpening angles. Highly recommended for both beginners and advanced users.
- Leather Strop Kit: Offers the final polish to achieve that razor-sharp finish.
Insert image of recommended sharpening products here. Each product has been thoroughly tested in my workshop, and I can confidently say that investing in top-quality sharpening tools will transform your woodworking projects.
Conclusion: Embrace the Art of Sharpening for Masterful Woodworking
In woodworking, as in life, the smallest details can make the biggest difference. Regular, careful sharpening not only enhances the performance of your tools but also inspires a deeper connection with your craft. By investing time and care into maintaining your cutting edges, you embrace a tradition of quality and artistry that defines true woodworking mastery.
Now it’s your turn—grab your favorite sharpening tool, set up your workstation, and rediscover the joy of perfectly sharpened edges. Whether you’re crafting a new piece of furniture or simply restoring an old heirloom, remember that every precise cut starts with a sharp tool.
Ready to take your woodworking skills to the next level? I invite you to leave a comment below sharing your sharpening tips and experiences. And if you found these insights helpful, don’t hesitate to share this post with fellow woodworkers and DIY enthusiasts. Every cut, every edge, and every project is a step closer to mastery!
Happy sharpening, and may your work always reflect the passion and craftsmanship that you put into every project!
For further reading and detailed product reviews, check out our additional resources here.